Leading Methods for Optimizing Steel Fabrication Processes for Maximum Efficiency
From meticulous design intending to embracing advanced innovations, the quest for maximum performance in steel manufacture involves a diverse strategy. Allow's explore just how these methods can transform steel fabrication processes, paving the means for unmatched effectiveness and competition in the market.
Efficient Layout Planning
In the realm of steel construction processes, effective and critical design preparation plays a pivotal duty in improving manufacturing operations and taking full advantage of operational performance. The format of a steel fabrication center directly influences the efficiency of operations, material flow, and worker efficiency. By thoroughly developing the plan of machinery, workstations, storage space areas, and product handling tools, firms can considerably decrease unnecessary movement, decrease material dealing with times, and enhance the overall production procedure.
An efficient layout plan takes into consideration factors such as process series, closeness of workstations, material handling routes, and safety and security regulations. It intends to produce a structured and logical circulation of activities from resources intake to the end product dispatch. With efficient design preparation, firms can eliminate traffic jams, minimize manufacturing downtime, and enhance the overall operational efficiency of the steel fabrication procedure.
Moreover, a well-thought-out design plan allows far better usage of available space, enhanced communication in between employees, and enhanced safety and security methods within the center. Generally, spending time and sources in establishing a reliable design plan can yield significant advantages in regards to boosted performance and expense financial savings for steel construction companies.
Advanced Reducing Technologies
Making use of advanced modern technologies in steel fabrication processes improves accuracy, effectiveness, and overall manufacturing high quality. Advanced cutting modern technologies play an important duty in improving operations and optimizing the construction procedure. Among one of the most prominent advancements in this area is the execution of laser cutting systems. Laser cutting deals unrivaled accuracy, permitting for complex layouts and intricate shapes to be reduced with marginal product wastage. Furthermore, plasma reducing technology has additionally revolutionized steel construction by enabling swift and specific reducing through electrically conductive products. This technique is especially effective for reducing thick steel plates with speed and accuracy. Water jet cutting is one more innovative modern technology that makes use of a high-pressure stream of water to cut with numerous kinds of materials, including steel, with remarkable precision. By including these advanced reducing technologies into steel manufacture processes, suppliers can dramatically increase effectiveness, minimize manufacturing times, and inevitably enhance the quality of their items.
Automated Welding Equipments
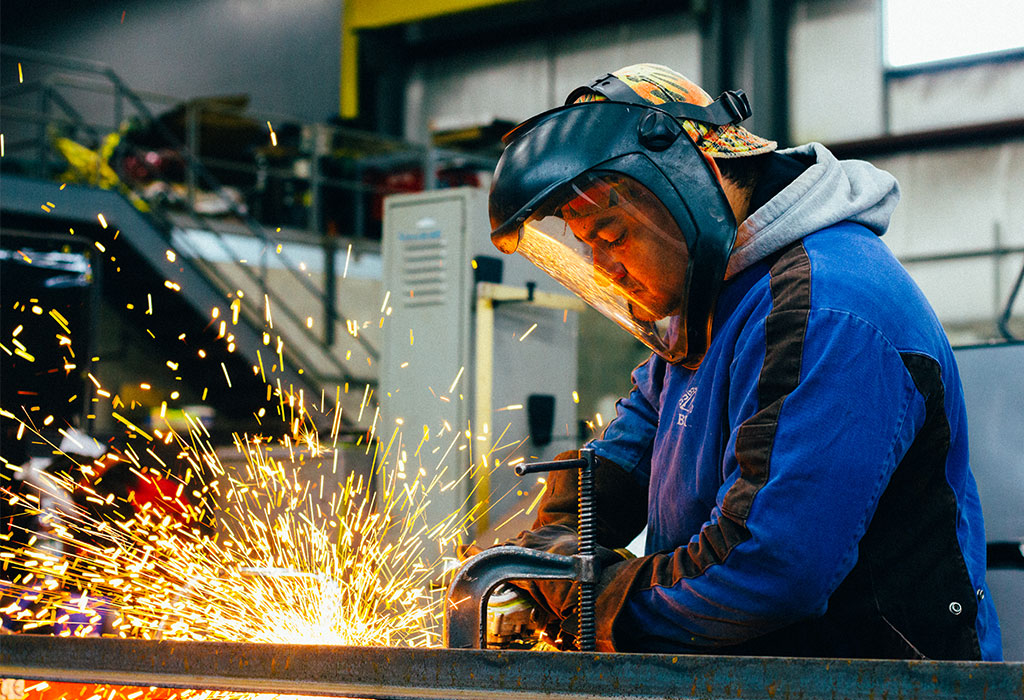
One of the essential advantages of automated welding systems is their ability to keep a high degree of precision throughout the welding procedure. The accuracy offered by these systems makes sure that welds are uniform and fulfill the needed requirements, resulting in stronger and extra dependable steel frameworks. Furthermore, automated welding systems minimize the threat of human mistake, leading to less defects and rework.
In addition, these systems can manage complicated welding tasks easily, consisting of welding in tight areas or on curved surfaces. This convenience makes automated welding systems suitable for a wide variety of steel manufacture applications, from massive commercial projects to complex custom-made designs. Overall, the implementation of automated welding systems in steel fabrication procedures substantially enhances effectiveness, top quality, and overall job end results.
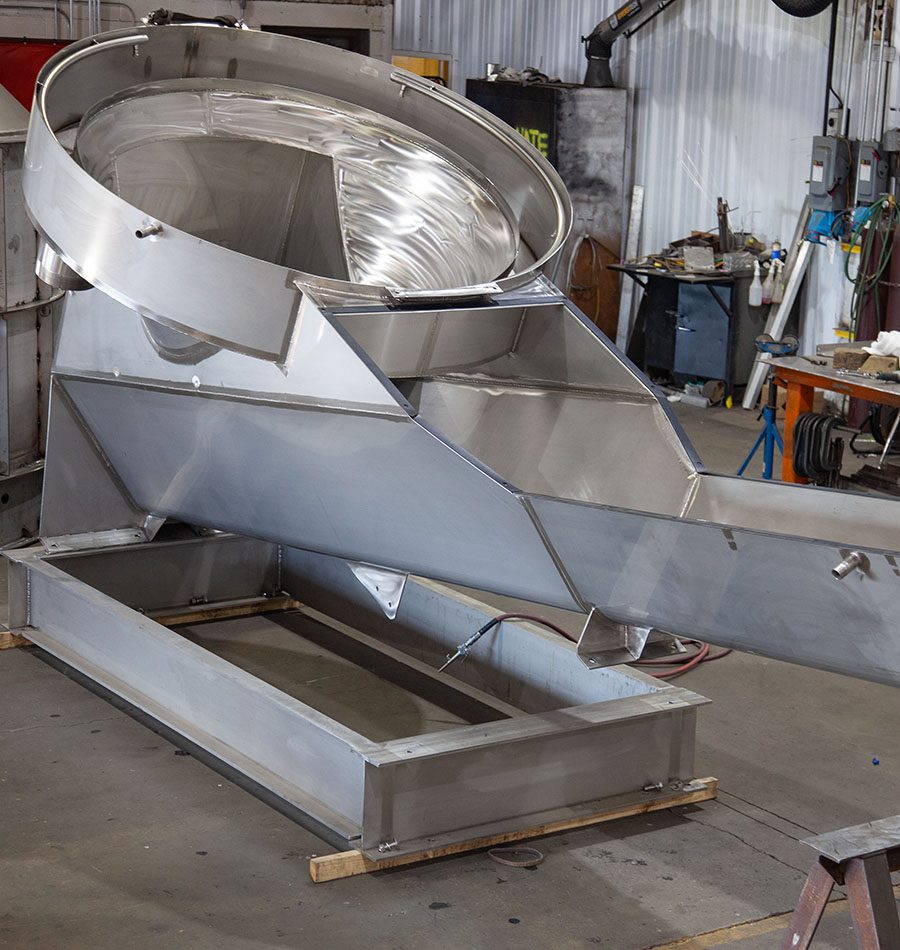
Inventory Monitoring Solutions
Enhancing functional effectiveness and improving procedures, effective inventory management remedies play a vital role in enhancing steel fabrication procedures. By implementing robust supply management systems, steel manufacture companies can make sure that the right materials are offered when needed, lessening disturbances and hold-ups in manufacturing timetables. Using sophisticated software application services permits for real-time tracking of supply levels, enabling precise projecting of material demands and stopping stockouts or overstock situations.
In addition, supply monitoring options aid in decreasing carrying view costs connected with excess supply and boost capital by straightening supply degrees with real need. By classifying products based on usage regularity and urgency, fabricators can focus on purchase and storage room allotment, even more improving operational performance. In addition, applying barcode or RFID technology helps with accurate stock tracking and simplifies the tracking of product movements within the facility.
Continual Process Enhancement
To build upon the gains made with efficient supply management options, the focus currently moves in the direction of driving constant procedure renovation within steel manufacture operations. Continuous process enhancement is a methodical method aimed at enhancing performance, minimizing waste, and increasing overall quality throughout the fabrication process. By applying a society of continual improvement, steel manufacture companies can determine bottlenecks, streamline operations, and maximize sources to optimize productivity.
One trick aspect of continuous visit site process improvement in steel construction is the regular evaluation and analysis of production processes. This entails event feedback from workers, monitoring key efficiency indications, and recognizing locations for improvement. By leveraging data-driven understandings, firms can make educated choices to drive significant adjustments that favorably influence procedures.
In addition, embracing lean production principles can significantly contribute to process enhancement in steel fabrication. steel fabrication melbourne. Techniques such as worth stream mapping, 5S company, and Kaizen occasions can help eliminate non-value-added activities, systematize processes, and promote a society of development and constant understanding within the organization
Verdict
To conclude, optimizing steel construction procedures for maximum efficiency needs careful planning, making use of advanced cutting innovations, carrying out automated welding systems, handling stock properly, and constantly improving procedures. By integrating these approaches, suppliers can boost productivity, minimize costs, and enhance total efficiency in the steel manufacture industry.
Via reliable format planning, business can get rid of bottlenecks, decrease production downtime, and enhance the total operational performance of the steel fabrication procedure. steel fixing.
Utilizing sophisticated modern technologies in steel fabrication processes enhances precision, efficiency, and total manufacturing quality. official source By integrating these advanced cutting modern technologies into steel manufacture procedures, makers can significantly boost effectiveness, reduce production times, and inevitably improve the top quality of their products.
Overall, the execution of automated welding systems in steel fabrication procedures dramatically improves efficiency, quality, and overall task end results.
One trick element of continual process enhancement in steel fabrication is the regular review and analysis of production procedures. (Alpha reo)